- BY nwmcadmin
- POSTED IN Plastic Injection Molding
- WITH 1 COMMENTS
- PERMALINK
- STANDARD POST TYPE
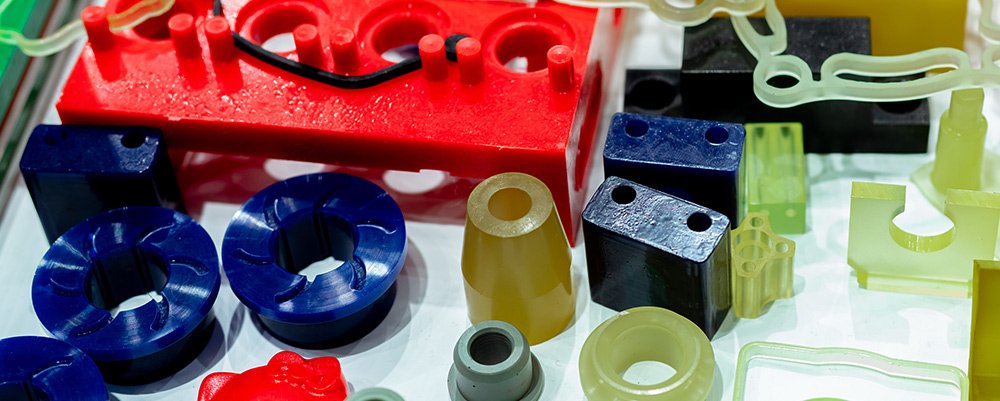
Plastic injection molding is a widely used manufacturing process for creating plastic parts of various sizes and shapes. Injection molding parts have become ubiquitous in our daily lives. From the plastic components in cars and appliances to toys and medical devices. If you have a product idea, it may interest you to learn if you can make it through injection molding, what it would cost, and how to go about designing it. Read on to learn more.
Injection molding parts
People create injection molding parts through a process that involves melting plastic pellets and injecting the molten material into a mold cavity under high pressure. Once the plastic cools and solidifies, you open the mold and eject the part. Injection molding is a versatile manufacturing process that can produce complex, intricate parts with high precision and consistency. Some of the most common products created through injection molding include automotive components, medical devices, household appliances, and consumer products.
What is the cost of injection molding parts?
The cost of injection molding parts can vary widely depending on several factors. This includes the size and complexity of the part, the type of plastic used, and the volume of parts produced. Generally, larger parts with more intricate geometries will require more expensive molds and longer cycle times. This can drive up the cost of the finished product. The type of plastic used can also impact the cost of injection molded parts. Some materials will be more expensive than others. Additionally, the volume of parts produced can affect the per-part cost, with larger production runs generally leading to lower costs per unit.
You will first need to pay for the mold to build it, which will be the largest upfront cost. Based on size and complexity, this can range from a couple thousand to tens of thousands of dollars. Once you build it, however, parts can run from a few cents to a few dollars. Again it depends on the size and complexity.
How to design plastic injection molding parts
Designing plastic injection molding parts requires careful consideration of several factors to ensure that the final product meets the desired specifications. It also requires that you can produce it efficiently and cost-effectively. Here are some key guidelines to keep in mind when designing plastic injection molded parts:
Design for manufacturability:
To create injection molded parts that can be produced efficiently and consistently, it’s essential to design with the manufacturing process in mind. Consider factors such as the size and shape of the part, the number of cavities in the mold, and the type of plastic to be used.
Use appropriate wall thickness:
The wall thickness of a plastic injection molded part is crucial to its structural integrity and manufacturability. It’s essential to balance the desired strength and stiffness of the part with the ability to fill the mold cavity and cool the plastic efficiently. In general, thicker walls are stronger, but they also take longer to cool, leading to longer cycle times and higher costs.
Optimize gate location:
The gate is the point at which the molten plastic enters the mold cavity, and its location can impact the part’s strength, aesthetics, and manufacturability. Choosing a gate location that minimizes the appearance of weld lines, maximizes the part’s strength, and facilitates efficient mold filling is essential.
Consider draft angles:
Draft angles are tapers incorporated into the design of plastic injection molded parts to facilitate their removal from the mold. Draft angles are essential to prevent the part from sticking to the mold and causing damage during ejection. People generally recommend using draft angles of at least one degree per side.
Test and iterate:
Designing plastic injection molded parts is an iterative process that involves testing, analyzing, and refining the design to achieve the desired result. It’s essential to work closely with your injection molding partner to test and refine the design throughout the development process.
This may seem like a lot to think about, especially if your project is in an early stage. But these are things that the engineers at Rex Plastics consider every day when designing parts for our clients. You do not need to know the ins and outs of making a plastic part run smoothly in an injection molding machine. Leave that to us!
Parts of an injection molding machine
An injection molding machine consists of several key components. Each of which plays a crucial role in the injection molding process. The hopper is where plastic pellets are fed into the machine. At the same time, the screw is responsible for melting and homogenizing the plastic. The nozzle controls the flow of plastic into the mold cavity. At the same time, the clamping unit holds the mold in place and applies the high pressure needed to inject the plastic. Other components include the mold, which you can custom-design for each part. The cooling system helps to solidify the plastic.
How Rex Plastics can help
Rex Plastics can help you design and create your product using injection molding. We’ve been doing it for our clients for over 50 years! In addition to injection molding, we also build molds, prototypes, and offer secondary options to plastic parts such as pad printing, assembly, 3d printing, and more. Reach out to us for a quote today!
1 Comments