- BY nwmcadmin
- POSTED IN Plastic Injection Molding
- WITH 0 COMMENTS
- PERMALINK
- STANDARD POST TYPE
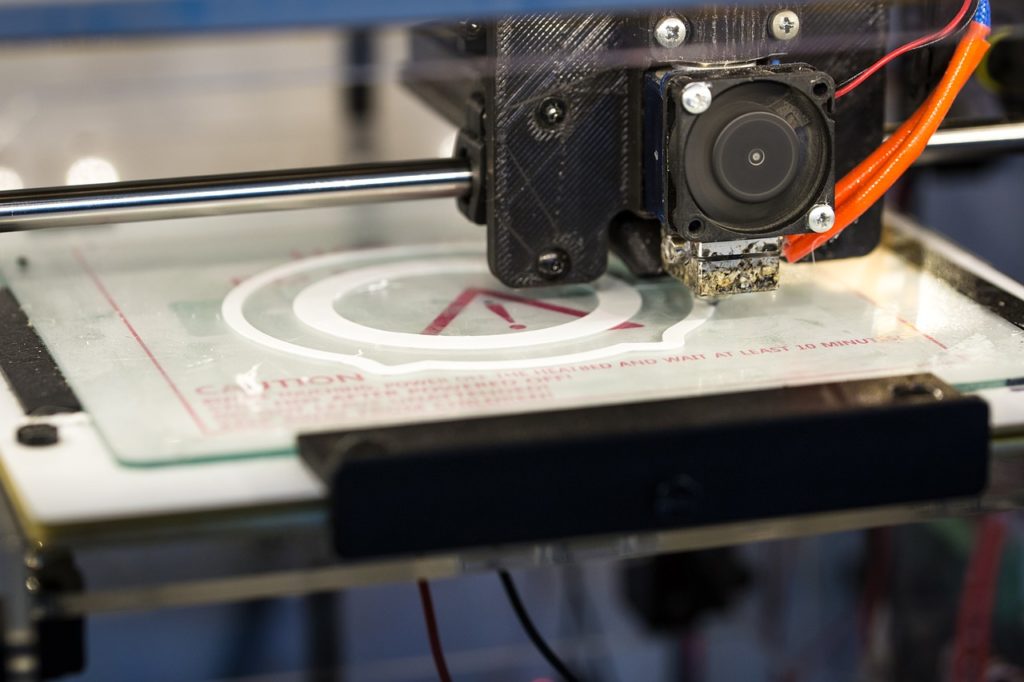
Injection molding parameters are not something you would be expected to know about unless you worked in injection molding. But when preparing a machine, an injection molding parameters sheet must be closely followed to avoid bad parts or damage to machines.
What are injection molding parameters?
Parameters are guidelines or rules, so for an injection molding machine, parameters are the specific settings for multiple aspects of their operation to run for a certain part. These parameters must be followed for the plastic material to flow smoothly through the machine and into the mold and to create a part without flaws such as sinkage, warping, or flash.
Why are injection molding parameters important?
Parameters for injection molding are important to set and follow so that parts are created with minimal errors. This saves money for the molder and the customer alike and ensures less waste. It is also important for the machines, as parameters that are not followed can cause excess wear and tear on injection molding machines and require extra maintenance.
Five important parameters for injection molding production
There are several important parameters to follow in injection molding. Five of these are:
1. Injection pressure
Injection pressure is the force the machine injects molten plastic into the mold cavity. This impacts factors such as material flow, part filling, and dimensional precision. A judiciously controlled injection pressure ensures uniform distribution of the melted polymer within the mold, minimizing the risk of defects like voids, sink marks, or short shots.
2. Injection time
Injection time determines the duration over which molten plastic is propelled into the mold cavity. A precise injection time is essential to ensure proper filling, packing, and cooling of the molded part. Too short an injection time might lead to incomplete part formation or inadequate material packing, resulting in structural weaknesses or surface imperfections. Conversely, a prolonged injection time could raise production costs and extend cycle times unnecessarily.
3. Injection temperature
Injection temperature refers to the temperature at which the polymer material melts and subsequently injected into the mold cavity. The choice of injection temperature significantly influences the material’s viscosity, flow characteristics, and overall molding process. A well-controlled injection temperature ensures consistent material flow, proper filling of intricate mold features, and optimal surface finish. Deviating from the ideal temperature range can lead to a host of challenges, from incomplete part formation to thermal degradation of the polymer, jeopardizing the mechanical properties and aesthetics of the end product.
4. Hold pressure and time
Hold pressure and time play a crucial role in shaping the outcome of the manufacturing process. Once the mold cavity is full of molten plastic, the machine applies hold pressure to keep the material in place as it cools and solidifies. This pressure ensures that the material maintains its intended shape and dimensions, minimizing the risk of shrinkage, warping, or other defects. The duration of the hold time is equally vital, allowing the material to settle and fully conform to the mold’s intricate details.
5. Back pressure
Back pressure is the resistance applied to the molten plastic as it moves from the injection unit into the mold cavity. This counterforce helps ensure consistent melting, homogenization, and removal of any trapped air or moisture within the material. By adjusting the back pressure, operators can influence the material’s flow characteristics, viscosity, and overall molding process. Striking the right balance is essential. Excessive back pressure can degrade the polymer or lead to overpacking. While insufficient back pressure might result in incomplete part filling and surface defects.
Contact Rex Plastics for an injection molding quote
We are an experienced company that knows the parameters of the injection molding process very well. With over half a century in the industry, Rex Plastics can meet your injection molding needs with precision and affordability. Reach out to us for a quote today!