- BY nwmcadmin
- POSTED IN Plastic Injection Molding, Plastic Injection Molds, Product Development
- WITH 1 COMMENTS
- PERMALINK
- STANDARD POST TYPE
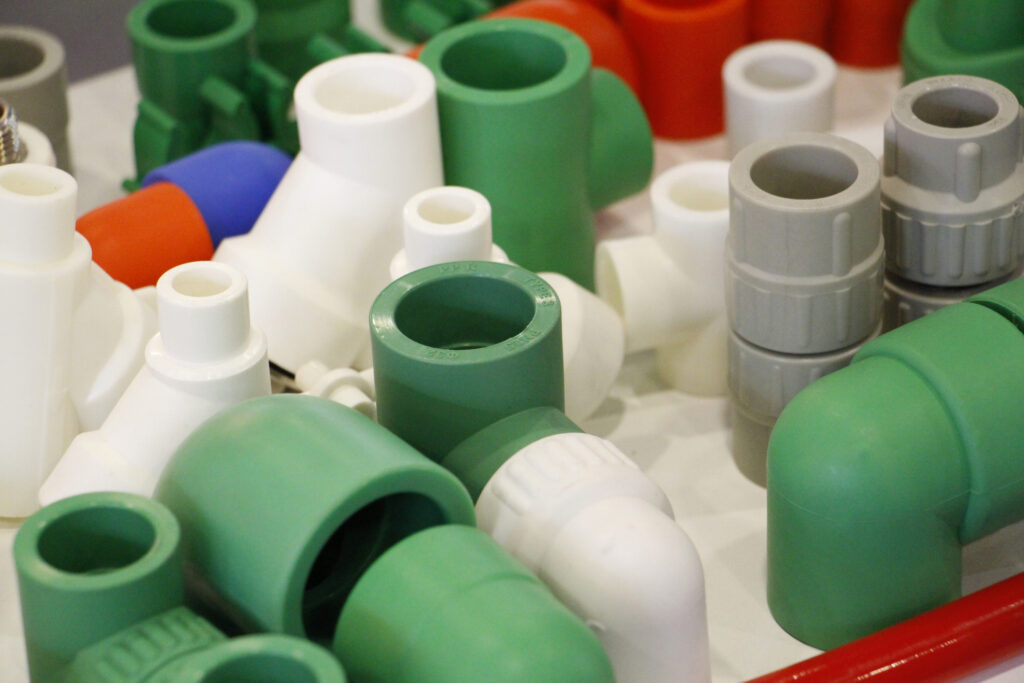
When making injection molded plastic parts, there are many things that can go wrong. It’s vital to tune injection molding machines and molds for parts to the right specification to prevent such errors. At Rex Plastics, we understand the importance in producing the highest rate of quality parts that we can. Minimizing rejected parts saves time and money—both for us and our customers. Flash is one of these defects, and we have years of experience in understanding how to reduce flash in injection molding.
In the image to the right, you can see flash around the edges of the shape.
Understanding Injection Molding
Plastic injection molding is a common manufacturing process that involves injecting molten plastic into a mold cavity. It allows for the production of complex parts with precision and efficiency. Under high pressure, molten plastic is injected into the mold, cooled, and solidified to create the final product. This process offers advantages like intricate design capabilities and fast production cycles.
What Is Flash in Injection Molding?
In the process of injection molding, flash can occur in the final product. Flash is a very thin section of plastic that can appear around the edges of a part. It is a very weak layer of plastic that may break easily. Some parts can tolerate a minimal amount of flash, but too much could hinder the intended use of certain parts, on top of making them more unsightly.
The Main Causes of Injection Molding Flash
Flash is the result of excess molten plastic leaking out around the edges of a mold. This forms into the thin plastic flap on the edge of a part known as flash. Injection molding is a process that requires very precise tolerances for every aspect of a machine’s cycle. Several factors can contribute to the occurrence of flash. One common cause is inadequate clamping force, which can result in the mold not being tightly sealed, allowing plastic to escape. Insufficient mold venting can also lead to flash by trapping air or gas inside the mold cavity, causing excess material to be forced out. Inaccurate injection parameters, such as excessive injection pressure or speed, can cause the plastic to escape through small gaps in the mold. Poorly designed or worn-out molds with improper parting line clearances may also contribute to flash formation.
How to Prevent Flash in Injection Molding
For a manufacturer trying to learn how to reduce flash in injection molding, these factors must all be considered. To minimize flash, it is crucial to carefully monitor and control clamping force, ensure proper mold venting, optimize injection parameters, and maintain molds in good condition. On top of that, it’s vital to have good quality control in case flash starts to occur on parts that were previously without it. That way, making adjustments as needed can assure that we run as part with as few rejects as possible.
Minor amount of flash can be trimmed from a part, but this requires additional time and labor in the production of a single part.
Contact Us for Injection Molding Services
At Rex Plastics, we have decades’ worth of experience in creating a plastic part that suits our customers’ needs. Reach out to us for a quote today!
1 Comments