- BY Rex Plastics
- POSTED IN Plastic Injection Molds
- WITH 96 COMMENTS
- PERMALINK
- STANDARD POST TYPE
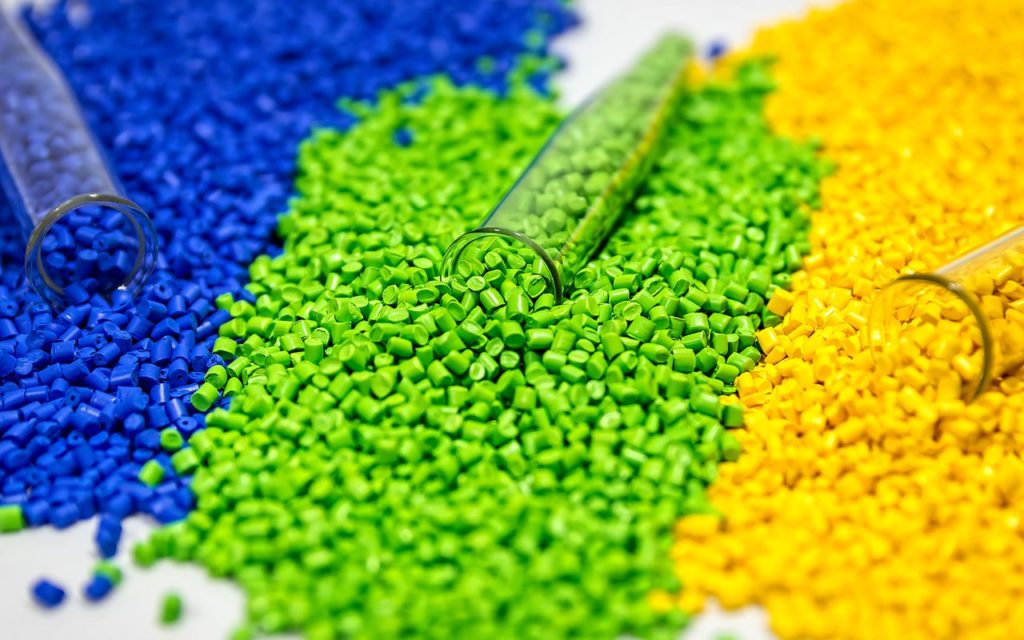
Injection molding cost can range anywhere from $100 to $100,000+ depending on the scope and intricacy of the project. A small and simple single-cavity plastic injection mold usually costs between $1,000 and $5,000. Very large or complex molds may cost as much as $80,000 or more. On average, a typical mold that produces a relatively simple part small enough to hold in your hand costs around $12,000.
But at least to some degree, asking what plastic injection molding costs is a lot like asking, “How much is a car?” Will your mold be a Pinto or a Porsche? And don’t forget that the price of a mold is just the beginning. To determine overall plastic injection molding costs for any project, you have to consider raw material, operation, and repair costs later down the road, too.
Is injection molding expensive?
The start-up costs for a large run can be expensive, but the price for the project becomes better and better as you continue to produce. If you’re looking at price per unit, plastic injection molding is one of the cheapest, most cost-efficient forms of manufacturing. With injection molding, the more units you create with your mold, the cheaper the price per unit becomes.
The determining factors in the cost of your mold are a combination of the part size, complexity, material, and anticipated quantities. For instance, if you wanted 1,000 washers per year, we would recommend a single cavity mold, meaning it makes one washer per machine cycle. In that case, the mold would probably be $1,000-2,000.
However, needing 100,000 Xbox controllers every month is a different story. For this requirement, we would recommend building a 12-cavity hardened “family” mold, which would make four Fronts, four Backs, and four Button Trees every cycle. Of course, this type of mold comes with a cost. You’d better have $60-$80,000 or more to invest!
These examples are extreme, but they illustrate the range of costs to anticipate. Your particular part will most likely fall somewhere in between that. At Rex Plastics, our molds average around $12,000.
What factors determine the cost of plastic injection molding?
In order to understand what the injection molding cost of your project may be, you need to understand the process and factors that will affect the price of your project.
Cost of equipment
There is a range of machines used for injection molding. The cheapest option is a small desktop injection molding machine perfect for in-house projects. A small desktop injection molding machine is the most cost-effective choice for producing low volumes of parts.
If your project requires large industrial molding machines that are operated by a service provider and large manufacturers, you’re looking at spending anywhere from $50,000 to $100,000+. Unlike the small desktop injection molding machine, these larger machines require professionals who can operate, maintain, and monitor the machine.
Cost of mold
Material selection is another consideration in determining what plastic injection molds cost. Any plastic product made from fiberglass-filled material, for example, will wear down most common molds. Only a mold made from hardened tool steel can withstand injection molding with fiberglass-filled material.
For most projects, there are three main methods for making molds or tooling.
- Computer numerical control (CNC) machine: At Rex Plastics, we primarily focus on hardened tool steel for our CNC mold-making process, but there are a number of materials suitable for CNC machines. Various metals and plastics, foam, glass, and even wood can be used to create products using different machines. Less common materials often require specialized equipment, such as hot wire or plasma cutters. CNC machines are an ideal solution for many different production jobs. From simple to unique, one-off products that require a high degree of precision and detail, CNC machines are a great fit as the process allows for accuracy down to a fraction of a millimeter.
- Electric discharge machine (EDM): EDM machines are better for very complex mold designs. By using a workpiece and a tool electrode, EDM machines can create highly accurate designs. Separating the workpiece and tool electrode is a dielectric fluid that causes recurring current discharges. These discharges are what shape the workpiece electrode to create the mold.
- 3D printing: 3D printing is the most cost-effective way to produce injection molds quickly. For 3D printed molds, there is much less equipment and professional labor needed. 3D printing can save you a lot of time and money. This method allows for a design to be tested and run a trial on the end-use material before actually investing in tooling for mass production.
Cost of injection molding material
Materials used in injection molding are plastics, specifically thermoplastics. There are hundreds of thermoplastics, but the most common thermoplastics used in injection molding are:
- Polypropylene
- Polyethylene
- Acrylonitrile Butadiene Styrene (ABS)
The cost of the material you use for your project is usually decided by the design, the material chosen, and the amount you need to complete the project. Here is a quick chart explaining more about each thermoplastic material, their features, common applications, and price per pound.
Type of Thermoplastic Material | Unique Features | Common Applications | Price per pound |
ABS | durable, lightweight | electronics, keyboards, phone hardware, LEGO bricks, drainpipe systems, kitchen appliances | $1.30 |
polyethylene | flexible, impact-resistant, leech-resistant, moisture-resistant, recyclable | food packaging, milk jugs, toys | $1.20 |
polypropylene | leech-resistant, flexible | Tupperware, kiddie pools, toys, utensils, car batteries | $0.90 |
polystyrene | warp, shrink and impact resistant | compact disc cases, packaging applications, household appliances | $1.00 |
nylon / (POM) | heat-resistant, durable | high-ware parts, quick-release buckles, gears, hand cranks | $2.20 |
polycarbonate | impact resistant, optical clarity, vulnerable to chemicals | automobile headlights, bulletproof glass, eyeglasses, greenhouses, DVDs, mobile phones | $2.30 |
Cost of service
The last thing to consider when pricing out your injection molding cost is the cost of service or professional labor you will need. Professionals can help you set up the necessary equipment to create molds and your products. During the process, they’ll be able to replace defective parts and monitor the progress of the overall process.
Plastic injection molding price guide
As a full-service plastic injection molding company that manufactures molds from conception to completion, pricing for each job we fulfill can vary dramatically.
However, we know injection molding cost estimates are critical to any successful project.
That’s why we’ve compiled the following price guide to help you budget for your mold. The injection molding cost examples are categorized by type (Rapid Prototyping, Insert Tooling, High-Production Tooling), and degree of difficulty (Basic, Intermediate, Advanced).
Planning your next project
If you have a target price established for your parts, tell your mold builder. They can design the mold accordingly and plan for the right number of cavities to achieve that price. The more cavities (or parts made per cycle), the less expensive the parts will be, also allowing for higher output.
While you don’t need to know every detail about the types of molds available, it’s always a good idea to come prepared. Supplying the basics to your mold builder will help them build the best tool for your project. We recommend that you find a mold maker who also has production capabilities. The production company won’t want to build an inadequate mold because they know they must use it.
If you’re thinking of outsourcing your mold-making overseas, consider all of the factors in bringing the mold to optimum production standards outlined in this American Mold Builders Association article. You might be surprised to learn the true cost of offshoring!
Whatever your project requires, Rex Plastics can help you decide whether you need a Ferrari or a Fiat.
Contact Rex Plastics to discuss your plastic injection mold needs
how much would a console mold cost and how many would i need? Same with controllers… do i need enough to make 100,000 a month?
Jake,
That is impossible to say without looking at the design, but as a general rule of thumb if you need 1,000 or more per year injection molding is worth looking at.
What would be the rough cost of a mold for a single cavity helmet? Full or open face? Very simple bare bones design?
Andrew,
Without seeing the specific design it’s difficult to give an estimate. Sometimes even small design features can add thousands to the cost of the mold. If you have a drawing we could provide a free quote.
Looking for price to make a mold for single hardhat and a mold for optical face shield.
Interested in disc golf disc mold …have u ever made any
Tyler,
We have not made any golf disc parts specifically but that is well within our capability. Please contact us for a free quote if you are interested.
I needed 1000 unit of enclosure (approx size 100 x 100 x 23 mm, fillet corner radius 20), Finishing should be fine as much as possible. I have seen the mould manufacturing costs a lot, is there any other way to manufacture enclosures at lower cost.
I’d be interested in finding out about plastic molded 9mm projectiles. There would have to be a denser plastic chosen, so there is enough recoil generated by the exiting projectile to cycle a semi-automatic pistol reliably.
Jason,
Thank you for the request for quote, I appreciate the opportunity. I don’t know what that would take. The highest specific gravity for readily available material is around 1.4. I would recommend researching how that compares to what is currently used. I know that some law enforcement agencies are using rubber bullets now but I don’t know if any sort of ejection assistance is used. Please contact us via service@rexplastics.com if you’d like to discuss further.
How much will a mold for HDPE lint roller (less than 70 grm in weight and 2 parts) for approx 500,000
shots cost?
Aashish,
Thank you for the request for quote, I appreciate the opportunity. The best opportunity we have to help make your project a success is if we have as much information as possible. If you could fill out our request for quote form our website it will be a big step in that direction. It includes questions about material, annual estimated production quantities, etc. as well as the option to upload drawings.
https://rexplastics.com/request-a-quote
Hi! I’m doing a school project and need soles and heels for a high heel shoe. Do you know how much that might cost?
If you would like to send any drawings you have to our contact email directly we can provide an estimate. service@rexplastics.com
Can you give a quote from a CAD file?
Eric,
Yes, we can quote from CAD, here is a list of formats we support:
.stp
.step
.x_t
.igs
.mcx
.sldprt
.dwg
.sat
I have an Idea…know nothing about this process, but here it goes. I wan’t to make a tool that will need Insert Molding? I know it’s a pricey operation, but to make it a durable and lasting tool it will have to be. I’d also like to have 6 to 8 tools made per cycle of the mold. the product would only be approx 5 to 6 inches long and 3/4 inch wide and approx 1/4 inch deep (approx). any idea (general idea) what this process would cost? I know there are many more details for plastic and metal applications, but a round about idea for a the mold would be helpful. Thank you.
Chris,
Thank you for the inquiry, I appreciate the opportunity. Without seeing the geometry it’s difficult to estimate cost. Our pricing guide can give an indication of cost, although it does not giving multi-cavity pricing.
http://rexplastics.wpengine.com/injection-mold-price-guide
For more accurate information please fill out our request for quote page and upload any drawings you have.
http://rexplastics.wpengine.com/request-a-quote
“On the other hand, if you are going to need 100,000 xbox controllers every month, we would build a 12 cavity hardened “family” mold which made four Fronts, four Backs, and four Button Trees every cycle, and you’d better have $60-$80,000 or more to invest.” is the 6o-8o,ooo dollars a yearly investment or a monthly investment?
The $60-$80,000 is a non-recurring expense to build the mold. Once the mold was built you would just pay for production parts as need. Probably around $1 per set at that point.
Hi, Do you also provide molding with rubber or any other elastic material? Is it (NRE and price per part) usually more or less expensive than plastic ?
tx, offer
We do mold with thermoplastic elastomers, which are still considered a plastic. It is more expensive than a lot of other types, and could add $.50 for a 100 gram part when compared to ABS.
I’m considering syringe barrels to be injection molded. About 3 mL and 6 mL (two different sizes) with qty of 20,000 per month for now. Actually syringe barrels without the thread, but with luer male at the end. Just empty straight (slightly tapered). Material PP.
Thank you for the inquiry. That does sound like something we can help you with. If you could please fill out our request for quote page on this site we can provide a quote. You can upload drawings there as well.
I want to buy injections.
Afan,
Thank you for your interest, do you have drawings or prototypes that we can quote from?
I’m glad you mentioned having a target price ready before designing a mold. I have a few things I want to start molding, but I hadn’t thought about a price yet. I can see how that would make a big difference in how they would plan how many parts to make.
Scott,
Thank you for the comment. We would be happy to look at whatever projects you have.
Do you guys sell 2nd hand moulds?
Curtis,
Out of respect for our customer’s IP we do not sell 2nd hand molds. Thank you for the inquiry.
Would like to mold adult male lacrosse stick heads, wondering how much each can cost, or how much a plastic injection machine would cost.
Thank you for the inquiry. That does sound like something we can help you with but would need more information. Can you provide drawings or a link to a similar product? If so please send them to service@rexplastics.com
Hello,
When submitting CAD specs to you or any injection mold company, do you recommend a Non-Disclosure Agreement be signed to protect a project?
Johnny,
Thank you for the inquiry. Non-disclosure agreements are common in manufacturing so any molder you choose should not resist signing one unless it’s determined to lack certain exclusions and the ability of the molder to disclose information to third parties with written permission. Molders will often need to involve third party companies in order to provide a quote.
Bottom line in regards to NDA is whether or not you trust the molder. If they are a legitimate company that has been around for a long time, they’re probably not stealing people’s ideas. If you are naturally a cautious person or something doesn’t seem right with the molder, you’ll feel better having one in place. Hope this helps, let us know if you have and NDA you’d like us to review or if you would like to look at the one we use.
I’m working on a school invention project and I need to know how much a mold for a half-pipe like design would cost. The thickness of the mold needs to be 1.5 inches, it is 1.5 feet high (bottom to top), 5 feet wide (left to right) and is 20 feet long (front to back). If you can estimate the price to the nearest thousand, that would be great. Thank you.
Hunter,
That product would be too large for us, and would likely need to be extruded. Try searching http://www.thomasnet.com for a large capacity plastic extruder.
I’m working on a school project, I was wondering how much it would cost to make a mold that contains 25 cavities, the part is kind of cylindrical and I was planning to have it made out of high density polyethylene. It has a hole straight through the part with an inside diameter of 0.515″ and an outside diameter of 0.670″ for 0.773″ of the height and an outside diameter of 1.340″ for the remaining 0.327″ of the height, the height is 1.100″ total. This is the link to the photo: https://drive.google.com/file/d/0BxyuyPDgKAbnMXdHbE1GeTA5bms/view?usp=sharing
https://drive.google.com/file/d/0BxyuyPDgKAbnN0xMSjJkNzdIUE0/view?usp=sharing
Thank you for the inquiry. Mold balancing plays an important role in injection molding, because of that we would recommend a 24 cavity mold. The parts are divisible in pairs with that amount and will run much better. The ballpark estimate for a cold runner mold that size would be $15-$20,000, and the part price would be under $.09 each for 20,000 parts ordered.
How much does a customized molder cost that is almost as big as a hand? 🙂
Kelsey,
Thanks you for the inquiry. That’s difficult to say without seeing the part. Small details in the design can make big differences in cost to manufacture. If it is a simple design with no undercuts and the surface doesn’t require polishing, you could perhaps get a mold built for $5-$8,000. Here is a link to a pricing guide for further reference. https://rexplastics.com/injection-mold-price-guide
Hi
I’m trying to get a project started and luckily I found the guides and explanations here, good stuff. With the guide my estimate is somewhere between 15 000 to 30 000.
What I have is four different geometrical round shapes of varying face counts with some small extruded borders between the faces. They’d be hollow so they’d be cut in a symmetrical manner so that two printed halves can be glued together to form a whole hollow sphere. All spheres are around 7,5 cm in diameter, about 3 inches, and half that in height due to them being halves. Additionally they’d have holes in specific places on the spherical surface but that could be drilled aftetwards, so just some sort of mark where the holes are supposed to be would be sufficient.
I understand that the small extrustion between the faces of the spheres could be an issue when removing the part from the mold, so they would not be a necessity. The geometrical shapes are just a collection of planar faces which create a sphere.
What would be the most logical approach if I wanted to create all four?
All on one mold? Each geometrical type with their own mold?
Then capacity wise,
10 000 a year?
100 000 a year?
I think I’ve exceeded 30 000 by a factor of 2 already, haven’t I?
Simon,
Thank you for your inquiry. It’s difficult to say, but you might be about right. Features that will effect tooling cost are the finish you would like on the parts (polished is more expensive than textured), and where the drilling marks are located. If there are undercuts created by them in relation to the direction the part will need to be ejected out of the mold, moving cores would need to be designed into the molds, which will significantly increase the cost. If these concerns could be worked out, we could probably build two molds to shoot these sets for $30-$60,000. If you would like tighter figures, we would need to see drawings or prototypes. Thanks again for the inquiry.
Hi,
Would you be able to create a mold for a golf bag, and provide a quote?
Approximately 35″ tall, with a diameter of 11.5″ x 10″. I’d also like to include dividers in the middle.
Thank you.
Unfortunately this product is too large for us. The largest footprint we can mold is approximately 100 square inches, and the tallest piece around 10″.
Hello,
Just so I’m clear, you would charge for the creation of the mold, and then create the parts as needed/requested? You would see me back a finished product correct – as in you supply the materials, ship, etc? Thank you.
Yes that is correct. After we build the mold (that you own), we store it here and run parts from it when you send us a PO.
Hello,
I have designed a product that I believe the best way to manufacture will be through injection molding. I cannot share too much, but for the sake of this comment lets imagine that it is a hollow box with 1/4″ walls, 1 face missing, and that it is 1′ 8″ W x 1′ 11″ L x 1′ 3″ H.
Now I understand that pricing is complex so I won’t ask you for a quote without sending the file, and I will assume that the mold will cost no less than $50,000 which is fine. My questions are below:
– Considering the dimensions of the extents, is it possible to create a family mold with multiple units? What would be the maximum units per mold? And around how many could be banged out per day (again assume its a 1/4″ wall box as stated above for now)?
– How long does the process of making the mold take (assuming the design and specs are ready)?
– Do I have to pay the full amount immediately, or can it be paid in installments?
– If I were to send over a .dwg file for a quote, are you legally bound by confidentiality?
Thank you in advance!
George,
Thank you for the inquiry. This product is too large for us but I will try to answer your questions.
-You can have a multiple cavity mold made for this part. If you built a four cavity mold you would need at least a 5,500 ton molding machine (and about $200,000 for a domestically made mold).
-With that mold you would probably get four parts every 2 or 3 minutes.
-A single cavity mold would still be over $50,000.
-Normally toolmakers will ask for 50% down with the remainder due once samples out of the mold are approved.
-Toolmakers and molder are not bound to confidentiality unless you have them sign a non-disclosure agreement.
Hopefully this helps, good luck!
Thanks for helping me learn more about plastic injection molds. I didn’t know that molds should be made from harden steel if a product needs a fiberglass filled material. I’m interested to learn how these molds could be made, especially of the steel mold needs to be really precise.
Thanks for this post, somewhat it helped me understand more about plastic injection mold and an estimation on how much it costs.
I was wondering how many times your molds can be used? if i were to get a basic insert tooling mold would you be able to give me an estimate of how many times it could be used?
Thank you for the inquiry Ali. All of our molds have a lifetime guarantee so even if your mold wears, you won’t see a repair bill from us. Generally speaking a hardened steel mold or insert should last 100,000 cycles or more.
Hi,
what are the estimated costs of a mold for a part with snap fit connections compared to the same part but instead of snap fit connections holes for bolts?
Rienk,
Thank you for the inquiry. That’s difficult to estimate without more information, but generally speaking snap fit connections will add $500-$1,000 to the cost of a mold.
How much would making a mold for a jackson pratt bulb that is two times the regular JP size.
Nicole,
Thank you for the inquiry. A Jackson Pratt bulb is blow molded, not injection molded. Please see this article for more explanation.
https://rexplastics.com/plastic-injection-molding/the-many-processes-of-plastic-part-manufacturing
Hi, thanks for your contribution on Injection molding . I have basic knowlegde on mold design and would like to know how can I estimate overall mold dimensions based on part dimensions, considering one cavity mold and and no side actions. Also would like to know how can I estimate the approximate size of a slider for a side simple hole. Thanks for you support. Much appreciate. Regards
First you locate and orient the part in the tool, which mainly depends on where/how you intend to gate it. For all gate types except center, you should have at least 0.75-1.00in of space between the sprue and the edge of the cavity. Once you have a cavity layout (assume centered sprue), determine its bounding box. Any space off-center will need to be mirrored on the other side of the sprue and included in this bounding box. In a sense, you’ll always be sizing a mold for two cavities unless you’re center-gating. For smaller molds under 12in per side (in the parting plane), you can get away with leaving 2in of space all around this bounding box. This space is occupied by the ejector housing, return pins, and leader pins among other things, all of which would interfere with the part cavities and/or their ejection. You may need extra space for cooling lines as well. For larger molds up to 24in per side, you’ll want at least a 2.5in perimeter.
As for plate thickness, leave at least 0.5in of steel between the upper and lowermost cavity extremities and the backsides of the cavity plates/cores. Depending on part geometry, you might need up to one full inch above and below the cavities for water lines.
Small sidenote, plan on leaving at least 0.250in of metal around all water lines. If not maintained properly they’ll eventually corrode thin walls. This consideration has occasionally led us to quoting larger mold bases.
Riser height will depend on how far the ejection needs to push your part before it’s completely free of the cavity and any cores. Completely free in this case meaning pushed all the way out/off so that there’s no chance it’ll get hung up on anything.
For slides, start by sizing the slide face. This is the block which will have the undercut detail cut into it. The face doesn’t need to be much larger than the undercut itself, but it should be rectangular or circular just for ease of manufacturing and assembly. The surrounding part geometry could factor into this too, if the undercut is in a cramped spot or located near/on curved surfaces. Leave perhaps 0.375-0.500in of steel behind the undercut detail (same idea behind determining cavity plate thickness) and assume a 0.50-1.00in perimeter on either side of the face for other hardware like guide rails, and 1.0-2.0in above and below the face for wear plates, heel blocks and bolts. The slide may well take up more space than your cavities, and drive the mold size and plate thickness all by itself.
It’s worth looking into the mold base CAD libraries out there, such as through PCS. They’ll generate full, downloadable 3D CAD of their offerings based on the specs you plug into their forms.
Rex Plastics
Hi,
Thank you for all the valuable information laid out on your site. My company has created molds and manufactured exclusively overseas, but I have tried to bring my business back stateside many times and have always found it difficult, biggest issue being MOQs. When creating a new product as a small business it’s difficult to run thousands or tens of thousands of units on a first run for an unproven product. My question is, after the mold is produced what is the average MOQ? What is your typical floor? What are the determining factors for the MOQ?
Thanks much
We do not have minimum order quantities, but there are set up fees amortized into each order so the cost effectiveness of low quantity orders is a decision left to our customers.
Hi am new here,
after I submit the CAD file will I pay $60 we part or I don’t understand.
after making mold what part will I pay for again?
Thank you for the inquiry. If you submit CAD drawings we will provide a quote for the cost of the injection mold and production. Once the mold is built you own it and will only pay for production parts out of it. If the mold remains in our possession it comes with a lifetime guarantee. Hopefully this answers your questions.
The quality of your articles and listing is really attractive.
Thanks for the inquiry. This post helping me understand more about plastic injection mold and estimation on how much it costs. And I learned from your post what an injection mold is made of.
This post helping me understand more about plastic injection mold and estimation on how much it costs. And I learned from your post what an injection mold is made of
Hi,
Thanks for your valuable post… I really appreciate your great work. This post helped me understand more about plastic injection mold and estimation on how much it costs.
An injection mold is easily the most expensive part of the project, and can dramatically increase costs for small part runs. The main factors that influence the cost of an injection mold are the size and intricacy of the part, the material used, and the number of parts being produced.
Your estimate cost for a steel p20, one cavity, cold runner, polypropylene 30%Gf matrix, with sizes of: 660mm x 220mm x 200mm. Thanks.
Thank you for the request for quote, we appreciate the opportunity. The best opportunity we have to help make your project a success is if we have as much information as possible. If you could fill out the request for quote form on our website it will be a big step in that direction. It includes questions about material, annual estimated production quantities, etc. as well as the option to upload drawings or photos.
https://rexplastics.com/request-a-quote
I always enjoy reading quality articles by an individual who is obviously knowledgeable on their chosen subject. I’ll be watching this post with much interest. Keep up the great work…
Thanks a lot for sharing this awesome info. Your article is excellent and informative. I love to read your articles.i personally like all the points you explain and follow it. Everyone should read this awesome post, I will share with my friends. Keep it up with such great content
Would it be possible for me to request solely 2 units for my design initiative? They are quite large with a 1-meter diameter and 1.5-meter length. How much would it cost for the production of this?
Thank you for the inquiry. Unfortunately this product is too large for us. The largest footprint we can mold is approximately 100 square inches.
Please keep us in mind for smaller projects.
What is the largest LxWxH you can support?
Thank you for your inquiry. We can mold up to 100 square inches of product footprint with a maximum height of 9 1/2″.
If you wouldn’t mind, how much would you ball park the cost to produce the mold, and the parts, of a standard size plastic shopping cart? Needing 100,000-500,000 units per year. I appreciate your time.
Thank you for the request for quote, we appreciate the opportunity. Unfortunately this product is too large for us. The largest footprint we can mold is approximately 100 square inches.
Please keep us in mind for smaller projects.
hi, how much do you think it would cost to produce water bottles (let’s say around 10 000 bottles) with a simple desing
Eloi,
Thank you for the inquiry. Bottles are blow molded, not injection molded so we couldn’t answer that question. Here is a link to out knowledge base for more information:
https://rexplastics.com/knowledge-base/product-development
Much needed information about the cost of plastic injection molds as knowing the price details are greatly helpful for the business.
hi I’m doing a school project and I need to know how much it will cost to make a simple 3,109 volumed container 12×14 container for the base and 12×14 for 2 sides and 14×20 for the other so
12=l
14=w
20=h
Thank you for your inquiry. Here is a link to a pricing guide that will get you headed in the right direction.
https://rexplastics.com/injection-mold-price-guide
Rex Plastics, Inc
Hi, I am interested in creating 6 different plastic figurines, each one in a 6 and a 12 in size. would I need to purchase a separate mold for each figurine and size? These would be low production, at least in the beginning, for retail and online sales. Are there options to have them manufactured in color? For example, skin tone, clothing and hair color?
We could put multiple figurines in one mold but injection molding may not be the best process if you are anticipating low volumes. 1,000+ per year may start to make sense for injection molding, otherwise you may want to talk to a plastic prototyper or polymer casting company. We can mold them in any color, but the entire figurine would be the same color. If you have drawings you can attach them to our Quote Now link and we can provide a quote.
I really like reading good articles by someone who knows a lot about what they’re writing. I’m excited to see more from you. Keep it up!
how much does an auto-cleaning robot vacuum cost?
how much does an auto-cleaning robot vacuum mold cost? – it is about as big as a robo-rock
I’m doing a project and I was wondering how much would the injection mold cost for a width:10 inch length:15 inch height 3 inches the top lid would be the same dimensions.
A professional Academy for Web Development Courses In Multan.
Great insights on the importance of precision in manufacturing. As a Welding and cutting machine manufacturers , Weldarc India understands the need for accuracy in welding and cutting processes. Our machines are designed to meet the demands of modern manufacturing with enhanced efficiency and precision. It’s exciting to see advancements in the industry that push the boundaries of what’s possible. Looking forward to continued innovations in welding and cutting solutions that contribute to high-quality production outcomes.
This article helped me to know more about plastic injection molds and their cost estimation. I learned from your article what injection molds are made of.
This post helping me understand more about plastic injection mold and estimation on how much it costs. And I learned from your post what an injection mold is made of
This post helping me understand more about plastic injection mold and estimation on how much it costs.
wan’t to make a tool that will need Insert Molding? I know it’s a pricey operation, but to make it a durable and lasting tool it will have to be.