- BY nwmcadmin
- POSTED IN prototyping
- WITH 2 COMMENTS
- PERMALINK
- STANDARD POST TYPE
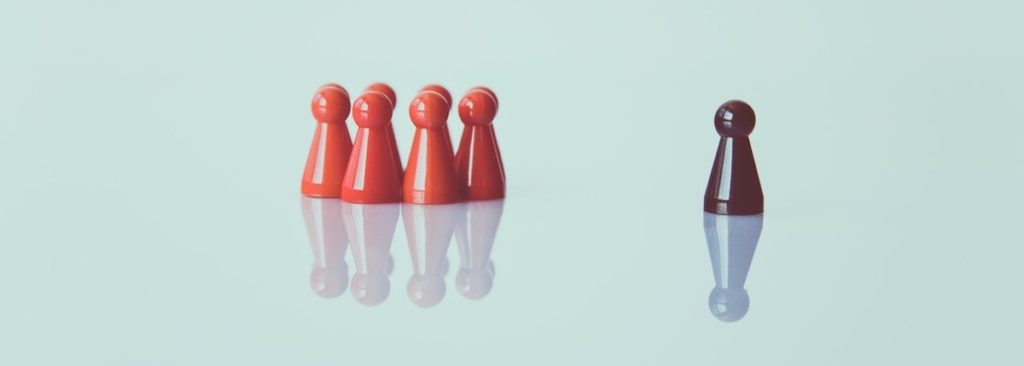
Do you have a great idea for a new product but need to test out a few different versions? Perhaps you need to create multiple examples of your product to show to investors. Either way, rapid plastic prototyping will help you develop your product and make the leap from design to mass production with lower risk. Learn what rapid plastic prototyping services are available, how each production method works, and which prototyping method is right for you.
What is rapid prototyping?
Rapid prototyping is the creation of a scale model of a physical part through an assortment of processes such as 3D printing, which is the most common process. The rapid prototyping process quickens the entire manufacturing process. Engineers and product designers use rapid prototyping for any kind of product development. However, they most often use it for plastic part development since most 3D printers can only use plastic.
What is the process for getting a product rapid prototyped?
Before you begin rapid prototyping, you’ll need a CAD design. Once you have that, the process typically looks like this:
- The prototyper will create the first iteration using a 3D printer, a CNC machine or vacuum casting.
- At this point, the prototype will need to be tested for fit and function.
- If the rapid prototype works, you can begin the mold building process.
- If the rapid prototype doesn’t work, then you’ll have to go back and tweak the CAD design and repeat steps one and two.
The process usually only takes only one or two full CAD/prototyping cycles before the plastic part works as desired and is ready for tooling. Of course, if you have stringent functionality or aesthetic requirements, there could be dozens of re-prototyping cycles.
Why use rapid prototyping?
Whether you’re developing a product in your garage or in a state-of-the-art manufacturing facility, it’s best practice to create at least one prototype.
Rapid prototyping is a professional service and comes with a price tag. So if you’re a handy individual entrepreneur and you’re able to fabricate your prototype by hand, you’re better off creating your own. After all, it will only cost you time and material expenditures.
However, if you’re creating a wholly plastic part, rapid prototyping will save a lot of time. A rapid prototyping company will sometimes only need a rough design to create a computer model and start the prototyping process.
Rapid prototyping is particularly suitable for original equipment manufacturers (OEMs) who need a high-quality prototype within a short amount of time and have the budget to pay for the process.
How much do rapid prototyping services cost?
The cost of rapid prototyping ranges anywhere from $75 to $1,000 or more and depends on the size and complexity of the plastic part. A small basic part with no post-production operations needed will sit on the lower end. A medium-sized part that requires minimal post-production work such as light sanding usually costs about $200. And a large and/or complex prototype can cost about $700.
See Rex Plastics price guide for more information.
When to use rapid prototyping: a case study
Rapid prototyping is ideal for plastic parts that need to be a precise size or fit. To achieve precision, engineers and product developers will often need to test the plastic prototype multiple times within a short period to meet deadlines. Rapid prototyping, as the name suggests, offers this advantage.
A protector cap, like those used for bolt heads, is a good example of a product that benefits from rapid prototyping because it must be an exact fit. Because the fitting must be precise, the mold needs to be equally precise.
Once you finish the rapid prototyping phase, it’s an easy next step to move on to production with injection molding.
Rapid prototyping software
While the software to actually print prototypes is usually proprietary and unique to the equipment used, here is a list of CAD programs used by rapid prototyping software to create models:
- Fusion360
- Solidworks
- AutoCAD
- Autodesk Inventor
- Mastercam
- Pro-E or Pro/Engineer
Different rapid plastic prototyping services
Which type of rapid prototyping process is right for me?
There are four major rapid plastic prototyping processes:
- 3D printing
- Fabrication/Machining
- Injection molding
- Casting
There are multiple methods within each of these processes. Each one offers distinct advantages and disadvantages that can be used to achieve the desired result. Production cost, quantities, materials needed, product size, and intended application will determine which one is best for you. Learn about each service in the next four sections.
(1) Creating a plastic prototype with 3D printing
People most often use 3D printing machines for rapid prototyping due to their affordability and versatility. There are dozens of different models and size capabilities. They also vary widely in the types of materials they can use.
3D printing covers a wide range of additive manufacturing techniques. The most popular methods for producing plastic prototypes are:
- Fused Deposition Modeling (FDM)
- Stereolithography (SLA)
- Polyjet
- Selective Laser Sintering (SLS)
- Multi-jet Fusion (MJF)
FDM plastic prototype printing
Among 3D printing processes, most people use FDM printing because these printers offer the most varied selection of materials, are the most affordable, and are the easiest to use.
FDM printing uses plastic filament made from:
-
ABS
- Ideal for automotive, aerospace, electronics, and consumer goods applications
-
PLA
- Best for colorful, non-functional prototypes that need to be fused with wood or metal composites or spliced with materials like carbon fiber
-
Nylon
- Perfect for prototyping gears and tooling
-
TPE & TPU
- Useful materials for rubber-like prototypes
-
PETG
- Most widely used material to prototype for water bottles and as an alternative to polycarbonate
-
Polycarbonate (PC)
- Best for industrial and engineering applications that require a prototype that can withstand wear and tear
This printing method uses an extrusion process to deposit plastic material in layers until the final product is created. It’s the most common type of 3D printing because you can heat the thermoplastics, bond them into any shape and as they cool down, they retain their shape.
FDM printing is most similar to a hot glue gun. The material comes in a solid stick that is melted down, squirted out, and then hardened into the desired form. The printer is able to calculate how much the plastic will squish and spread as well as accounting for cooling distortions.
Post-processing for FDM printing is similar to working with any wood object. There will be visible layer lines, and you’ll need to file the rough edges and possibly paint it too.
FDM printing is ideal for hobby and project printing in schools and at home. Many people use it to print knick-knacks, but the process also produces unique parts that people use in their daily lives such as one-of-a-kind mobile phone stands.
FDM printing offers a good balance of speed and detail. However, if you need a small detailed object, the SLA process is better.
SLA plastic prototype printing
Instead of applying filament in an additive manner, SLA 3D printing uses a vat that holds all of the resin needed to create a rapid prototype. Powerful lasers cure the resin layer by layer as the build platform pulls the semi-solid prototype out of the gooey resin.
SLA post-processing is much more complex than FDM printing because there will be a lot of excess resin. You can use isopropyl alcohol ultrasonic baths to remove the excess resin. To fully solidify, you’ll have to cure SLA prototypes with UV light.
SLA printing is more toxic than FDM printing. The resin vapor can irritate the respiratory system and the material can harm the skin.
Rapid plastic prototypes made with SLA printing can achieve an unsurpassed level of detail. Unlike FDM printing, which leaves visible layer lines, SLA printing produces a smooth finish. In most cases, SLA printing layer lines are only visible with a magnifying glass.
SLA printing is most often used for miniatures and props. This process is widely used for various prototyping purposes, especially within the medical, dental, and consumer goods space.
A major advantage of SLA printing is that it is suitable for investment casting. Investment casting is the process of building mold around your printed parts, which is then burnt out. Metal is then cast in the mold’s place. This process is common for jewelry making at home.
Polyjet printing
Polyjet printing is a proprietary process developed by Stratasys and is similar to SLA in that it cures liquid resin with light. At the same time, it is similar to an FDM machine because the print head moves and drops beads of resin to build the prototype. This combination reduces waste and makes for easier cleanup.
SLS plastic prototype printing
Like SLA printing, the power source for SLS printing is a laser. But instead of resin, a powder typically made out of nylon is used. Lasers are used to heat or pressurize the powder to form a compact and solid mass layer by layer. Once the whole object is formed, the excess powder is removed with a brush and pressurized air.
One of the advantages of using SLS is that you don’t have to worry about supporting the prototype. The powder supports the object during the fabrication process.
Both the material and print quality of SLS surpass FDM printing. SLS prototypes are typically more functional, flexible, and durable too. You can print full assemblies with this process, which eliminates the need to assemble parts after printing. Plus, you can even create products that would be impossible to assemble with traditional methods.
(2) Fabricating or machining a rapid plastic prototype
CNC machining and fabrication are other excellent methods for rapid plastic prototyping. These processes are fast, produce larger prototypes, and offer a wider surface finish selection than other types of rapid prototyping services.
CNC plastic machining and fabrication most often use the following materials:
-
ABS
-
PC
-
PP
-
POM
-
PMMA (Acrylic)
-
HDPE
-
Teflon
-
PEEK
Rex Plastics, an American-based, family-owned and operated plastic mold manufacturer offers CNC prototyping services for startups and established OEMs. Contact us to learn if CNC machining is right for your next project.
(3) Creating a rapid plastic prototype with injection molding
Injection molding is a unique process that not only produces prototypes but is also an ideal method for mass production.
Creating a plastic prototype using injection molding is much like mass-producing a part. Once a cavity is created, molten plastic is injected into the hollow space and rapidly cooled into a solid part.
Compared to 3D printing, plastic injection molding produces higher-quality surface finishes. Deep features, square holes, and living hinges, which are difficult to create with CNC machining, are also possible with injection molding.
Of all rapid prototyping services, injection molding is the slowest process because you must build a mold first. And as a result, it also has the highest upfront costs. As a rule of thumb, this method is best if you need 100 or more prototypes, or if you must evaluate the material and/or cosmetic properties of the final product. The most popular plastics for injection molding include:
-
ABS
-
PC (Polycarbonate)
-
Nylon
-
HIPS (High Impact Polystyrene)
-
PP (Polypropylene)
-
PE (Polyethylene)
-
PET (Polyester)
-
PETG
-
POM/acetal
-
Acrylic
-
ASA
-
PPA
Rex Plastics is a full-service plastic injection molding contract manufacturer. Contact one of our project managers today to learn more about this type of rapid prototyping service.
(4) Creating a rapid plastic prototype with vacuum casting
Vacuum casting, also known as Room Temperature Vulcanization (RTV) casting and urethane casting, is a three-step process.
First, you’ll need to create a master prototype using 3D printing or CNC machining. Once the master prototype is complete, it is suspended in a box and covered with liquid silicone rubber. A cavity is created within the liquid silicone rubber once it hardens and the master prototype is removed. Colored die and resin are poured into the cavity in a high vacuum chamber and cured. The silicone rubber mold can create 15-20 prototypes before it becomes useless. The entire process usually takes about two weeks.
Although you can’t get the level of detail that you can achieve with other rapid prototyping methods, vacuum casting is one of the fastest ways to mass-produce a plastic prototype. The process also requires a smaller upfront investment, relative to injection molding while still offering comparable quality and material selection. However, the prototypes are generally not functional and work best as visual models.
Rapid prototyping in China and overseas
Many American plastic part manufacturers outsource their rapid prototype development to overseas companies—most often to companies located in China—due to the low-cost service. Unsurprisingly, you get what you pay for, and there are several significant drawbacks to consider before you choose an overseas rapid prototype service.
Low-quality parts
Compared to American plastic prototype services, overseas companies do not adhere to the same quality standards. Outsourcing plastic prototyping services increases the chance that your rapid prototype will have flaws.
Limited accountability
If you do receive a low-quality part from your foreign rapid prototype provider, it can be very difficult to hold the company accountable. Perceptions of what makes good customer service are very different in other countries and you might have a hard time getting the right prototype at the right price.
Language barriers
Communication is essential during rapid prototyping, especially if your prototype requires re-prototyping. Many overseas rapid prototyping service providers do not have enough staff members that are fluent in English to adequately handle foreign orders. It’s common for designs to get lost in translation and prototypes to fail.
Patent issues
Copyright laws are very loose to non-existent in some overseas countries, which means you may no longer have exclusive rights to your patented design if it gets in the wrong hands.
Although low price rapid prototyping prices overseas can be tempting, the headache of working with a foreign company as well as the financial risk may not be worth it. If your design requires even a modicum of attention to detail, you’re likely better off keeping the rapid prototyping process onshore in America where there is a shared system of beliefs and you can hold the rapid prototyping service provider accountable. Learn why plastic manufacturers choose to reshore their prototyping services.
What to look for in a rapid prototyping company
Are you ready to begin the exciting journey of prototyping your idea? Regardless of whether your rapid prototyping service provider is located in America or abroad, you should find out how reputable the company is before you sign a contract. A good rapid prototyping company will:
- Consistently fulfill a customer’s needs
- Quickly respond to a customer’s concerns
- Offer rapid prototyping services at a reasonable price and to a reasonable standard
The next step
There are several ways to produce a plastic prototype and a near-infinite number of materials. The best method, material, and service provider hinge on the type of plastic part you need to make. Before you begin rapid prototyping, talk to an industry expert or project manager to plan your next project. Many rapid injection molding companies like Rex Plastics also offer free quotes.
This article is very useful there can be a lot of growth, thanks for this information provided
I’m curious to know more about the environmental impact of plastic prototyping and whether there are any sustainable practices or materials that can be used in the process. Are there any specific measures or alternatives that can help minimize waste and promote eco-friendly prototyping methods?
On another note, if you’re interested in exploring opportunities to buy and sell plastic scrap, I highly recommend checking Rawtechtade. They provide a convenient platform for businesses and individuals to trade plastic waste, encouraging recycling and reducing plastic pollution. It’s a great way to contribute to a more sustainable future while also benefiting economically. Have you ever considered joining a plastic scrap marketplace like this?