- BY nwmcadmin
- POSTED IN Plastic Injection Molding, Plastic Injection Molds
- WITH 1 COMMENTS
- PERMALINK
- STANDARD POST TYPE
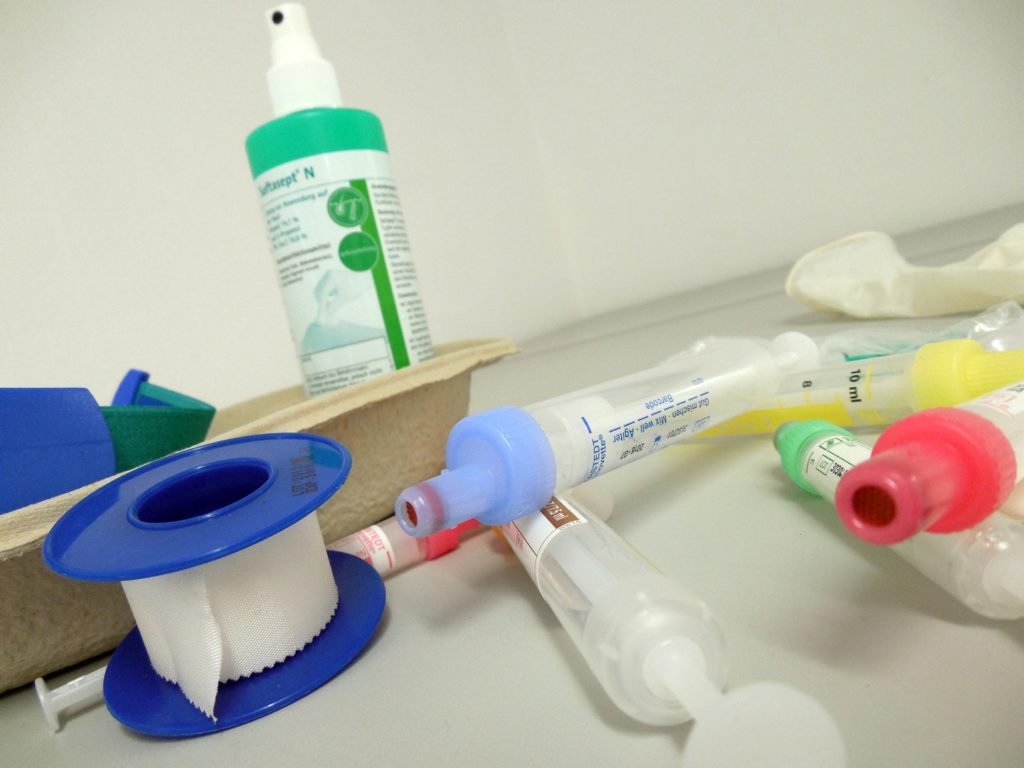
We have five decades of experience but are always looking for new and revolutionary ways for businesses to better utilize their products. For Rex Plastics, one example of this is the medical industry’s use of plastic injection molding. The accuracy of injection molding plays a critical role in achieving high precision and reliability in medical components. Additionally, the cost efficiency of injection molding makes it highly beneficial for large-scale production, significantly reducing the cost-per-part.
Medical applications for injection molding are numerous. They’ve completely changed the medical landscape — and there are more changes on the way. Producing high-quality parts is essential to ensure the reliability and compliance of medical components.
Introduction to Medical Injection Molding
Medical injection molding is a manufacturing process used to create medical devices and components with high precision and accuracy. This process involves injecting molten plastic into a custom-designed mold, allowing it to cool and harden into the desired shape.
Medical injection molding is a critical process in the medical industry, enabling the production of complex and sensitive medical components, such as surgical instruments, implantable devices, and medical device housings.
The use of medical-grade plastics, such as polyetheretherketone (PEEK) and polyethylene (PE), ensures that the final products meet the stringent standards for patient safety and regulatory compliance. These materials offer exceptional mechanical properties, biocompatibility, and the ability to withstand harsh environmental conditions, making them ideal for medical applications.
By leveraging the precision and reliability of medical injection molding, manufacturers can produce high-quality medical components that meet the rigorous demands of the healthcare industry.
What is medical injection molding?
Medical injection molding is the process of creating plastic parts and devices specifically for healthcare use. It involves injecting molten plastic into a custom-designed mold, where it cools and hardens into the required shape.
This process enables the efficient, repeatable production of critical components like syringes, diagnostic devices, surgical tools, and implantable components, which are essential in the healthcare industry.
Medical injection molding is tailored to meet the strict requirements of the healthcare industry, including biocompatibility, sterilizability, and high precision. The use of biocompatible materials ensures that these medical devices can be sterilized without losing their essential properties, thereby ensuring patient safety and broad applicability in medical settings.
It helps manufacturers deliver consistent quality while keeping production costs manageable — a key factor in modern healthcare.
Techniques Used in Medical Injection Molding
There are several types of injection molding processes used in the medical industry, each with its unique characteristics and applications.
- Plastic injection molding is the most common process. This method is highly versatile and cost-efficient, making it ideal for producing everything from syringe components to medical device housings. Read the specifics about this technique here.
- Insert molding is another specialized process (read the details here). This technique is particularly useful for creating medical devices that require the integration of different materials, such as surgical instruments with metal tips and plastic handles.
- Liquid silicone injection molding is a process that involves injecting liquid silicone into a mold to create flexible and biocompatible medical components, such as catheters and implantable devices. Silicone’s excellent mechanical properties and biocompatibility make it an ideal material for medical applications that require flexibility and durability.
- Micro molding creates extremely small, detailed parts, ideal for minimally invasive surgical tools.
- Other advanced methods, like gas-assisted molding and two-shot molding, offer solutions for complex designs or enhanced material performance.
Choosing the right technique is critical for successful, cost-effective medical manufacturing. Collaborating with an injection molding expert is essential to refine designs, select suitable materials, and optimize the manufacturing process through services like DFM analysis.
How is medical injection molding unique?
Medical injection molding stands apart because of the heightened standards required for healthcare products. Regulatory compliance, extreme precision, and contamination control all add complexity to the manufacturing process. This ensues patient safety by emphasizing the importance of material selection and regulatory standards.
Every stage — from material selection to production — must meet the rigorous demands of patients, healthcare providers, and regulators alike. Using FDA-approved materials is crucial in this context, as they enable injection molding to meet stringent regulatory requirements. This ensures that the produced parts are consistently compliant and suitable for various medical applications.
FDA Approval and ISO Certifications
Medical devices must meet strict regulatory requirements before they can be approved for use. In the U.S., the Food and Drug Administration (FDA) ensures medical products are safe and effective. In the medical device industry, regulatory compliance is crucial to ensure that all products meet stringent standards.
Manufacturers also seek ISO certifications, particularly ISO 13485, which defines international quality standards for medical devices. When manufacturing injection molded parts, it is essential to adhere to FDA and ISO standards to ensure the parts are compliant and safe for use in medical applications.
Achieving these certifications requires extensive quality assurance processes. Working with a supplier experienced in FDA and ISO regulations can help avoid costly delays and streamline the path to market success.
Precision
Precision is critical in medical injection molding. Parts must meet tight tolerances to function properly inside devices or the human body, ensuring optimal performance.
Even minor deviations can compromise safety. Advanced mold design, computer-controlled manufacturing, and thorough inspections help ensure ultra-high accuracy.
This level of precision supports innovation and reliability in medical equipment and components. Structural integrity is also crucial, as it ensures the produced parts can endure the demands of their applications, leading to fewer defects and enhanced performance over time.
Cleanrooms
Many medical products must be manufactured in cleanrooms — highly controlled environments where airborne particles, humidity, and temperature are carefully regulated.
Cleanrooms reduce contamination risks that could compromise a medical device’s performance or sterility. Additionally, cleanrooms protect medical devices from harsh environments. This ensures that materials like PEEK maintain their integrity and performance even under extreme conditions.
Depending on the application, cleanrooms may need to meet classifications like ISO Class 7 or 8. Operating in cleanrooms ensures that sensitive medical parts meet the highest safety and hygiene standards.
Materials
Material selection is crucial for medical injection molding. Choosing the right medical-grade plastic is essential, as these materials must be biocompatible, sterilizable, and able to withstand chemicals or repeated use. Selecting contaminant-resistant materials like silicone and polyethylene ensures the safety and effectiveness of medical devices and products.
Common materials include medical-grade polyethylene, polypropylene, polycarbonate, PEEK, and silicone. Each offers different benefits, from flexibility to chemical resistance. PEEK, in particular, is highly suitable for surgical implants due to its exceptional properties, such as resistance to harsh environments and dimensional stability under stress.
Extensive testing and validation ensure that the materials chosen can meet safety, performance, and regulatory requirements.
Common Medical Applications for Injection Molded Parts
Injection molded parts appear in a wide range of medical settings. Many medical devices, including disposable products such as syringes, IV components, and specimen cups, are mass-produced for sterility and affordability.
Surgical instruments like forceps, retractors, and scalpel handles benefit from plastics’ lightweight, ergonomic design. Additionally, the precision and consistency in the production of medical device components ensure reliable and effective medical equipment.
Diagnostic equipment housings are often molded to protect delicate internal electronics. Even implantable devices like orthopedic anchors and drug-delivery systems are increasingly created with medical-grade injection molding.
The versatility of plastics continues to drive innovation in healthcare.
Benefits of Injection Molding for the Medical Industry
Injection molding brings with it a number of advantages. One is scale; it’s easy to manufacture in volume, since plastic injection molding is easier than the casting and stamping methods often used with surgical steel. Additionally, it is a cost efficient manufacturing method, offering precision and the ability to produce high-quality parts that meet the stringent standards of the medical industry.
The raw materials are less expensive. Compliance is less onerous. The journey from concept to finished product is much faster.
Another consideration, given the rise of drug-resistant infections, is cleanliness. Traditional metal instruments must often be sterilized between uses, and a small slip-up or an instance of neglect can negatively affect patient outcomes and liability alike.
High-quality thermoplastic materials, such as polyetheretherketone (PEEK), are used to produce reliable medical devices due to their exceptional resistance to harsh environments and dimensional stability under stress. Something as simple as a single-use scalpel can have an outsized impact.
The Future of Injection Molding in Medicine
We’d be remiss if we didn’t also look ahead to what’s next in injection molding, especially as it relates to medicine. In many ways, the future isn’t as far off as it seems — and in some ways, it’s already here. Injection molding plays a crucial role in supporting the medical and pharmaceutical sectors by providing precision manufacturing and high-quality production capabilities.
We know this because our extensive work with startups reminds us on a near-daily basis that the next innovation is often percolating in someone’s mind, just looking for the right processes, plastic prototyping, and tools to become a viable product.
Among the developments we’re keeping an eye on:
- Wearables: Wearable and IoT (Internet of Things) devices are fast-growing segments that give their users near-instant access to vital signs, insulin levels, and fitness. Injection molding has found use here for housings, key components, and more.
- Pharmaceutical Plastics: Certain plastics and polymers aren’t merely relegated to devices. In fact, from prosthetics to implants, injection molding is taking on the capability of internal as well as external use.
- Emerging Processes: Post-molding processes are continuously growing and evolving, and nowhere is this more apparent than in medical applications. We’re also keeping tabs on the emergence of cutting-edge polymers that will allow for a wider range of applications than ever before.
Our commitment to providing turnkey solutions in custom plastic injection molding ensures that we can manage projects from initial design through to high-volume production, particularly focusing on the medical and pharmaceutical sectors.
Getting Started With Injection Molding
Given the wide range of available processes, requirements, and applications, each plastic injection molding company brings a different skill set to the table. Medical professionals rely on high-quality, precisely manufactured components that meet strict industry standards.
A telephone consultation with Rex Plastics can help determine if our American-made injection molding is the right fit for your next project.
If it is, we will shepherd your project from concept to prototype to finished product — and beyond. Partnering with an experienced manufacturer like Rex Plastics is crucial for successful medical device manufacturing. We utilize advanced manufacturing techniques, such as plastic injection molding, to ensure precision, cost-efficiency, and regulatory compliance. Contact us today to get started!
Frequently Asked Questions
Question | Answer |
How long does it typically take to complete a medical injection molding project? |
Timelines vary depending on part complexity, regulatory needs, and mold design. Simple projects can take 8–12 weeks from concept to production, while highly complex or regulated devices may take longer. |
Can medical injection molding accommodate custom colors for branding? |
Medical-grade plastics can often be custom-colored without compromising safety or compliance. However, additives must be carefully selected to maintain biocompatibility and meet regulatory standards. |
Is it possible to prototype parts before full production? |
Absolutely. Prototype molds allow for testing of part fit, function, and manufacturability before investing in high-volume production tooling. This helps reduce risk and speeds up development. |
Can existing metal medical devices be converted to plastic using injection molding? |
Often, yes. Many metal components can be redesigned in medical-grade plastics to reduce cost, weight, and risk of corrosion. A thorough engineering review is needed to ensure the plastic version meets all performance criteria. |
The blog “Plastic Injection Molding in the Medical Industry” provides a thorough exploration of the critical role that injection molding plays in manufacturing medical devices. The author effectively discusses the stringent regulatory requirements and the need for precision and reliability in medical applications. The insights into material selection and design considerations make this post an invaluable resource for professionals in the healthcare sector. Thank you for sharing this detailed analysis, and I look forward to more posts that delve into the intersections of plastics and healthcare innovation!