- BY nwmcadmin
- POSTED IN Plastic Injection Molding, Product Development
- WITH 0 COMMENTS
- PERMALINK
- STANDARD POST TYPE
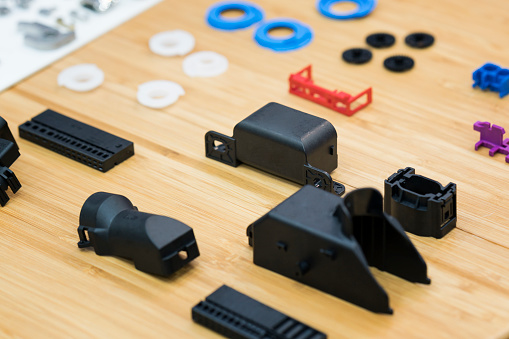
What is the Parting Line in Injection Molding?
An injection molding parting line is visible on all injection molded plastic parts. The two halves of a mold create a parting line between them when they clamp shut. While molds need to seal completely during the process, a thin visible line can always still be found on the final product. The mold design and type of plastic used determine the size and the line’s appearance.
How to Decide Parting Line in Plastics?
The location of a plastic parting line is determined both by mold function and part function. The parting line is where the mold opens, so easy ejection from that point is required. It may also be visible and affect the functionality of the final part.
At Rex Plastics, we will work to decide the most optimal parting line that allows for easy mold operation and a final product that is to your satisfaction. In the image to the left, the parting line follows the edge of the part designed and molded by Rex Plastics. This is where the seam of the mold was. It is often ideal for the parting line to be placed and designed around the edge of the part like this.
Why is there a Parting Line in Injection Molding?
An injection molding parting line exists because of how molds for plastic parts function. The mold has two halves that close together for plastic to be injected into the center. While the mold seals very tightly, the area around the seam will have a small parting line when the mold opens to reveal the part. It may be very minuscule depending on how tight the fit of the mold is, but the parting line is something that must be considered and planned for with every mold.
What are some Parting Line Challenges?
As with anything in the injection molding process, there are some challenges to plastic parting lines. Here are just a couple of common challenges injection molding specialists face with parting lines.
Parting Lines on Complex Shapes
Deciding a plastic parting line becomes more difficult with complex shapes. It might not always work to be down the middle of a part. Mold designers will find a location that meets the part designer’s needs and allows for easy production. The parting line could take on different shapes and does not need to be straight. It can also be placed around certain edges of the part or somewhere subtle where it will be mostly hidden in the final product.
Preventing Parting Lines on Liquid Silicone Parts
Liquid Silicone Rubber parts (LSR) are more complex to work with. Molten LSR fits into smaller gaps and can create more flash, or thin excess plastic, around the parting line. It is more difficult to get it right, but if it is designed well LSR parts will have a parting line that is smaller and harder to notice. These earbud covers (right) are made of LSR.
Have a Project in Mind? Let Rex Plastics Know!
Rex Plastics has experienced part and mold designers. We can work to build you a mold with a well-placed parting line. Not only that, but we also offer prototyping, pad printing, and many other services for startups and OEMs. Reach out to us for a quote today!