- BY nwmcadmin
- POSTED IN Plastic Injection Molding
- WITH 0 COMMENTS
- PERMALINK
- STANDARD POST TYPE
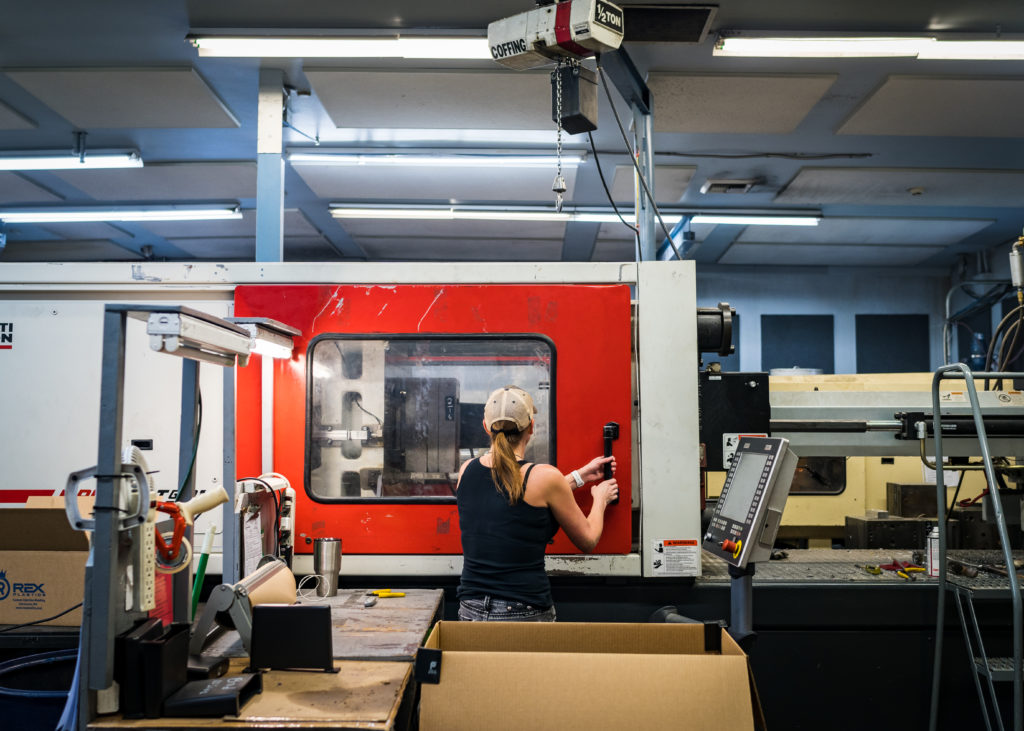
What is a sprue?
A sprue is a channel through which molten plastic flows into the mold. Specifically, the sprue is the entry point of the molten plastic, the vertical passage which plastic then flows through into runners and gates. In general, the entire assembly is commonly known as the sprue. The whole system is easily seen when looking at parts of a toy model. The actual pieces are the end product, produced in the mold cavities, and the connecting plastic is what cools inside the sprue and runners. This entire structure can be seen in the plastic assembly below.
Sprues and recycling
After the finished pieces are freed from the sprue, you can find yourself with quite a bit of plastic waste. This is often seen as one of the downsides of injection molding in this fashion. This leftover sprue, however, is not without its uses. It can be collected, melted down, and recycled into usable plastic, ready to go through the injection molding process again.
Hot runners
One alternative to conventional “cold” sprue and runner systems is hot runners. With hot runners, the general process is the same but in this case, the plastic is kept heated so that it never solidifies within the runners. This allows for much faster production and eliminates the need to collect and recycle the cooled plastic. To read more about the pros and cons of hot runners, check out our blog here.
Hot sprue bushings
Hot sprue bushings are heated bushings that keep plastic molten that would otherwise cool into a hard stem. Unlike hot runners, these bushings do not keep the runners or sub-runners molten. These hot sprue bushings help to reduce waste in this way and also reduce cycle times a bit because the sprue often takes the longest to cool. This process can be seen as an intermediary step between the convenience of cold runners, and the efficiency of hot runners.
What sprue is right for you?
As with most decisions, the design of your sprues, runners, and gates should be determined by the product being manufactured. Products being made with ABS, a common injection molding material, will require larger runners than some other materials like nylon. Other factors, such as the size and thickness of the product also have a major impact on the design of your runners. As a result, larger cavities will require larger and more precise gates, the final channel through which plastic flows into the mold.
Meeting your needs
With all of these choices and decisions, it’s important to partner with a manufacturer you can trust. Rex Plastics has the skill and experience to see your injection molding project through from start to finish. If you have questions, contact us today. And if you’ve got a project you’d like to get started with, you can request a quote now.