- BY nwmcadmin
- POSTED IN Plastic Injection Molding
- WITH 3 COMMENTS
- PERMALINK
- STANDARD POST TYPE
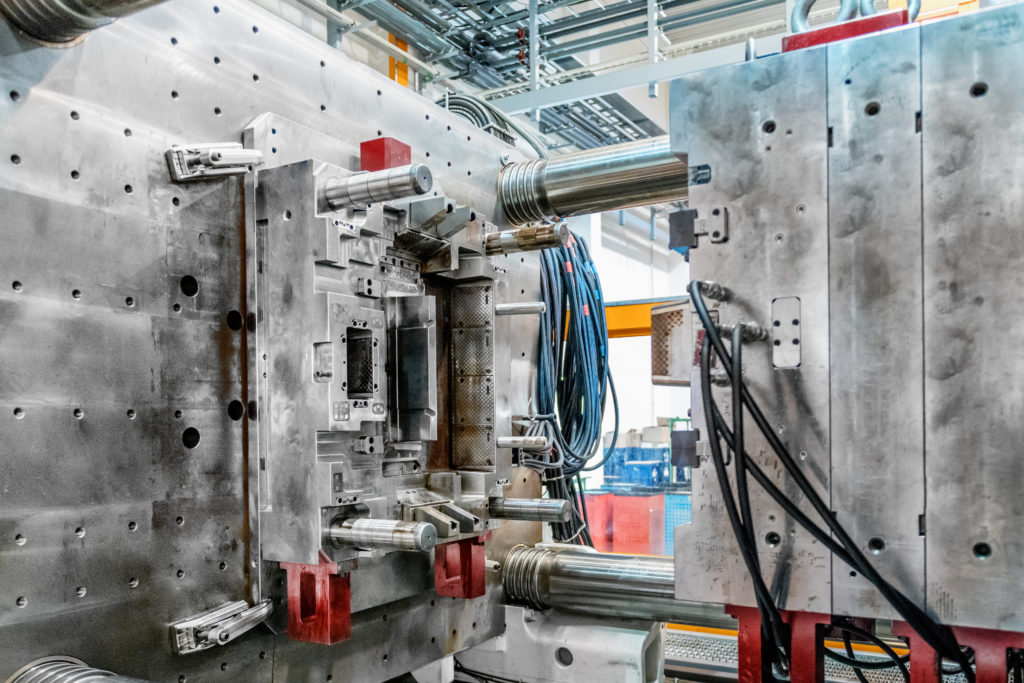
Since its inception in the 1960s, to its acceptance in the 1990s, the hot runner system has challenged tradition across the plastic injection molding business. With their increased cycle speed and decreased waste, hot runners are an attractive solution to many looking to diversify their injection molding process.
What is a hot runner injection molding system?
A hot runner system delivers liquid plastic to a number of mold cavities in order to create a plastic product. It is an injection molding assembly that uses a heated manifold to keep plastic in a molten state. This heated plastic travels from the molding machine nozzle through internal channels called runners and can be delivered directly into multiple cavities at the same time.
Hot Runner vs Cold Runner Injection Molding Systems
Today, most plastic injection molding is done in one of two ways; hot runner systems and cold runner systems.
While the two systems differ in a number of ways, one of the key differences between the two systems is that hot runners are able to inject plastic directly into the part cavity, whereas cold runner molds use a sprue and runners to channel the plastic into the mold cavities.
Hot runner molds eliminate surface imperfections and reduce waste, making them ideal for high volume production with high detail and smooth surfaces. However, they are more expensive and complex, leading to higher setup and installation costs. On the other hand, cold runner molds have lower manufacturing costs but result in slower cycle times and waste from runners that are difficult to recycle.
Understanding the strengths and weaknesses of both systems is crucial, as each lends itself to different products and production needs.
In general, hot runners are ideal for projects like:
- Cell phone cases
- Bottle caps
- Projects that require a high volume of inexpensive parts.
Cold runners are a good choice for:
- Electronic housings and coverings where blemishes can be hidden
- Keyboards
- Lower volume production
However, cold runner molds have limitations such as slower cycle times and waste from runners that are difficult to recycle.
Cold runners are, and have long been, the most commonly used runner system for plastic injection molding. Cold runners inject plastic into a sprue, a central channel through which plastic flows into the runners. As the name implies, the plastic cools in a cold runner system. It solidifies in the cavities as well as in the sprue and runners. The excess plastic must be cooled and removed each cycle, which slows down the cycle time.
In addition, plastic products formed using cold runners systems generally show more blemishes due to larger plastic entry points called gates. Hot runner technology significantly reduces waste and enhances productivity, making it ideal for high-volume production.
System Components and Functionality
A hot runner system is a sophisticated assembly designed to deliver molten plastic efficiently and consistently to the mold cavity. Here are their key components:
- Heated Manifold: The heart of the system, the heated manifold, maintains the temperature of the molten plastic, ensuring it stays in a fluid state as it travels through the system.
- Nozzles: These components direct the molten plastic from the manifold to the mold cavity. They play a crucial role in ensuring the plastic flows smoothly and accurately.
- Temperature Controller: This device regulates the temperature of both the heated manifold and the nozzles, ensuring consistent plastic flow and preventing any fluctuations that could affect the quality of the final product.
- Gate: The gate is the entry point where the molten plastic enters the mold cavity. It is designed to control the flow and prevent backflow, ensuring a smooth and efficient molding process.
- Runner System: The network of channels that connect the manifold to the nozzles and gate, the runner system, ensures that the molten plastic flows seamlessly to the mold cavity.
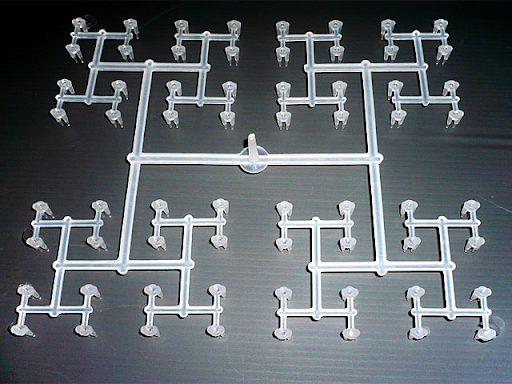
A sprue and runner system used with a cold runner for plastic injection molding
The functionality of a hot runner system can be broken down into several stages:
- Plastic Injection: Molten plastic is injected into the heated manifold.
- Temperature Control: The temperature controller ensures that the manifold and nozzles maintain the correct temperature.
- Plastic Flow: The molten plastic flows through the runner system and into the mold cavity.
- Gate Control: The gate regulates the flow of plastic into the mold cavity, ensuring consistent filling and preventing backflow.
Advantages
Hot runner systems offer several significant advantages over cold runner systems, making them a preferred choice for many plastic injection molding applications:
- Reduced Waste: Unlike cold runner systems, hot runner systems eliminate the need for cold runners, significantly reducing material waste and saving on material costs.
- Increased Efficiency: Hot runner systems can produce parts at a much faster rate than cold runner systems, thanks to their ability to maintain the plastic in a molten state and reduce cycle times.
- Improved Part Quality: The direct injection of molten plastic into the mold cavity results in parts with superior surface finishes and fewer defects, enhancing the overall quality of the final product.
- Increased Design Flexibility: This type of system allows for more complex part designs and geometries, providing greater flexibility in product development.
- Reduced Energy Consumption: By minimizing the amount of plastic that needs to be melted and cooled, hot runner systems can reduce overall energy consumption, making the injection molding process more energy-efficient.
Cold Runner Limitations
While cold runner systems have been a staple in the plastic injection molding industry, they come with several limitations that can impact efficiency and product quality:
- Waste Generation: Cold runner systems generate waste in the form of cold runners, which must be removed and disposed of after each cycle, leading to increased material costs and waste management challenges.
- Increased Cycle Time: The need to cool and remove the cold runners after each cycle can significantly increase the overall cycle time, reducing production efficiency.
- Limited Design Flexibility: The presence of cold runners can limit the design flexibility of parts, as the mold must accommodate the runners, potentially restricting the complexity of the part geometry.
- Increased Energy Consumption: Cold runner systems require more energy to melt and cool the plastic, leading to higher energy consumption and increased operational costs.
How does a hot runner injection molding system work?
Hot runners inject plastic directly into the cavities, as opposed to the sprue and runner system used in a cold runner system. Injection molds play a crucial role in the plastic injection molding process, with hot runner molds offering significant advantages such as reducing waste and improving production efficiency. One of the biggest advantages is that the plastic in the runners will never solidify. This decreases the cycle time, allowing for faster processing.
Another benefit of this system is a reduction in plastic waste, as the material does not harden until the mold is filled. The lack of a sprue system substantially cuts down on the amount of trimming required to smooth the final product. Hot runners operate through an additional manifold which is bolted to the mold assembly.
Major Hot Runner Systems Manufacturers
When considering the use of a hot runner system, it is important to understand the quality of its manufacturer. Internationally, Husky is one of the more well-known companies. The world’s largest brand name supplier of manufacturing solutions, Husky has a proven track record of delivering high-quality injection molding systems. The machines they produce can handle high volume and frequent use, while still maintaining a great deal of precision.
Other manufacturers include companies like Maenner and Mold-Masters. Research is imperative when choosing a manufacturer. Will they provide training and support? Are the hot runners assembled on delivery? Will the system come with the controller? Knowing the answers to these questions will help when choosing a supplier.
Building a mold for plastic injection requires a considerable amount of communication with the manufacturer. The molds and the hot runner system must be perfectly compatible, and this requires that both parties work closely during the design and manufacturing process.
Do I need to find my own hot runner system supplier?
In most cases, the answer is no. Your mold maker will already have a system supplier that they work with. The hot runner system is so highly integrated into the mold that mold makers will have a preferred supplier that they work with. Plastic injection molds utilizing hot runner technology minimize waste during the molding process, especially in multi-cavity setups.
It is important to talk to your service provider to learn which hot runner system manufacturer they use, and why. These systems work best when both companies have built a strong working relationship and have a good history of successful collaboration.
Hot Runner Price
Hot runner systems certainly have their advantages, but as we have discussed, they also come with a higher price tag. In general, you can expect to pay between $20,000 and $30,000 for a hot runner manifold, and another $5,000 for the controller.
Beyond this, the price for an entire system begins to vary depending on the number of zones included in the manifolds. These zones, also known as drops, are the injection points for the molten plastic. The more drops a system has, the more cavities can be filled at once, and the more the system will ultimately cost.
It is important to understand these costs when considering a hot runner system and to understand that these costs constitute an investment.
Types of Hot Runner Systems
When we talk about hot runner systems, we are actually talking about two distinct versions of that system. This difference primarily involves the style of the injection point. These two different injection point types are known as hot tip and valve gate.
Hot Tip Hot Runner System
Hot tip is the standard, general-purpose version of the hot runner system that we have discussed thus far. It is more economical than the valve gate system and is the most common hot runner system in use. Hot tip is ideal for mass production of simple parts and products.
Valve Gate Hot Runner System
A valve gate is a style of injection point featuring a mechanical valve that automatically closes when the machine injects plastic into the mold. This results in a smooth closure, leaving no visible nubs or abrasions on the surface of the product.
A valve gate system is ideal for products that need to look great, like in highly aesthetic projects where customers will notice. This system is even more efficient than the general-purpose hot runner, and as such, is more expensive.
Choosing a Hot Runner System
Selecting the right hot runner system for your injection molding needs involves considering several critical factors:
- Material Selection: The type of plastic you plan to use is a crucial consideration. Different materials have varying flow characteristics and temperature requirements.
- Part Design: The complexity and design of the part you intend to produce should guide your selection. These systems offer greater design flexibility, but it’s essential to ensure the system can accommodate your specific design requirements.
- Production Volume: Consider the production volume when making a selection. High-volume production runs can benefit significantly from the efficiency and reduced cycle times offered by hot runner systems.
- Budget: While hot runner systems can be more expensive upfront, they offer long-term cost savings through reduced waste and increased efficiency. It’s important to balance the initial investment with the potential long-term benefits.
- Manufacturer Support: The level of support and service provided by the manufacturer is crucial. Ensure that the manufacturer offers comprehensive training, support, and maintenance services to maximize the performance and longevity of your system.
By carefully considering these factors, you can select a system that meets your specific needs and enhances your plastic injection molding process.
The Future of Hot Runner Injection Molding
While there will always be a need for cold runner systems, it is clear that hot runners are the technology of the future, and more importantly, the present. The reduction in cycle time and the removal of runner waste solidify them as an indispensable component of modern injection molding.
Understanding that, it is important to know when to use one system or the other. With a greater awareness of hot runner systems, it becomes possible to make more informed decisions in the years ahead.
If you are considering an injection molding system and are not sure which is right for you, please contact Rex Plastics with any questions. If you already know what you’re looking for, request a quote and get started today!
Frequently Asked Questions
Question | Answer |
---|---|
How does a hot runner system impact color changes in injection molding? |
Hot runner systems can make color changes more challenging because residual plastic from previous batches can mix with new colors. Some systems have quick purging capabilities or special coatings to minimize material retention and speed up color transitions. |
What maintenance challenges come with hot runner systems? |
Hot runners require regular cleaning and inspection to prevent nozzle clogging, heater failure, and material degradation. Proper temperature control is crucial to avoid defects and minimize downtime for repairs. |
Are there any environmental benefits of using a hot runner system? |
Yes, they may reduce plastic waste by eliminating sprues and runners. They also lower energy consumption by reducing the need for re-melting scrap material, making them more sustainable over time. |
Can all types of plastic materials work in hot runner systems? |
No, some heat-sensitive plastics or thermosetting materials may degrade in hot runner systems. Engineers must choose materials with good thermal stability to ensure proper flow and prevent defects. |
How do hot runner systems affect mold design and complexity? |
Hot runner molds are more complex due to additional components like heating elements and temperature controllers. While this increases setup costs, it improves part quality, speeds up cycle times, and reduces material waste. |
The blog post on hot runner systems from Rex Plastics offers a clear and concise introduction to this essential technology in injection molding. The author effectively outlines the advantages of using hot runners, such as improved efficiency and reduced waste, making it easy for readers to understand their significance in the manufacturing process. I appreciate the author’s informative approach and expertise on the topic. I hope to see more insightful content from them in the future, as it greatly benefits industry professionals.