- BY nwmcadmin
- POSTED IN Plastic Injection Molds, Product Development
- WITH 0 COMMENTS
- PERMALINK
- STANDARD POST TYPE
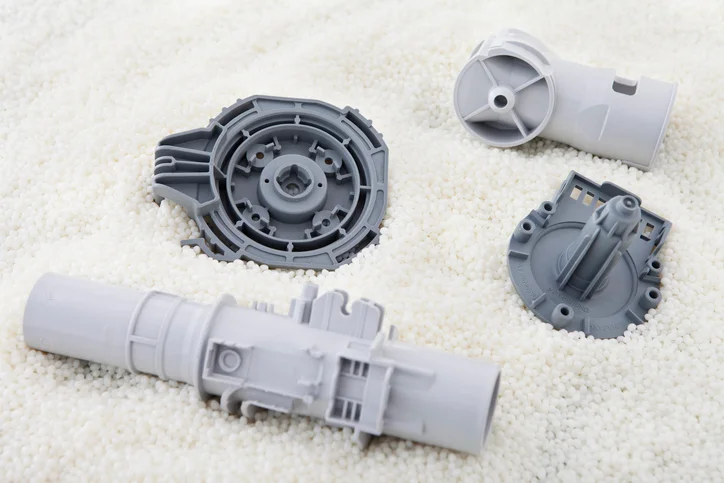
Polyoxymethylene (POM), commonly known as acetal plastic or acetal resin, is an engineering thermoplastic widely recognized for its superior mechanical properties, dimensional stability, and resistance to moisture and chemicals. In this blog, we’ll explore the defining characteristics of POM, its advantages in injection molding, how it compares to acetal resin, and the diverse applications that make it a staple material in many industries.
What is POM plastic?
Polyoxymethylene, abbreviated as POM, is a high-performance thermoplastic material prized for its exceptional stiffness, low friction, and high wear resistance. It is often used in precision parts that require tight tolerances and consistent performance under mechanical stress. POM is available in two main types:
- Homopolymer (POM-H): Offers superior mechanical strength, hardness, and rigidity, making it ideal for high-stress applications.
- Copolymer (POM-C): Exhibits better chemical resistance and lower thermal degradation, which is advantageous in wet or corrosive environments.
Key Properties of POM
- Low moisture absorption
- Excellent machinability
- High mechanical strength and stiffness
- Good resistance to abrasion and wear
- Excellent chemical and thermal resistance
5 Advantages of Polyoxymethylene in Injection Molding
Polyoxymethylene is a popular choice for injection molding due to its outstanding material properties and versatility. Here are some key advantages of using POM in injection molding:
- Dimensional Stability: POM maintains its shape and size under varying environmental conditions, making it ideal for precision applications.
- Low Friction: Its low coefficient of friction and self-lubricating properties reduce wear and improve the longevity of components.
- Chemical Resistance: POM withstands exposure to fuels, solvents, and other chemicals, ensuring durability in harsh conditions.
- High Strength-to-Weight Ratio: POM’s lightweight nature, combined with its mechanical strength, makes it a cost-effective replacement for metals.
- Ease of Machining: The material’s consistency allows for smooth machining processes, reducing production costs and time.
Polyoxymethylene vs Acetal Resin
While POM and acetal resin are often used interchangeably, it’s important to understand their nuances:
- POM-H (Homopolymer): Known for its higher strength, stiffness, and creep resistance, POM-H is ideal for applications demanding maximum rigidity and mechanical performance.
- POM-C (Copolymer): Offers enhanced resistance to hydrolysis, strong alkalis, and thermal-oxidative degradation, making it suitable for wet environments and food-grade applications.
Both variants are widely utilized across industries, but the choice between them often depends on specific application requirements, including chemical exposure and operating conditions.
What kinds of projects is POM best suited for?
POM is a versatile material that finds applications in numerous industries due to its unique properties. Some common applications include:
- Automotive Industry:
- Fuel system components
- Gears, bearings, and bushings
- Door handles and window regulators
- Electronics and Electrical Components:
- Insulating parts
- Connectors and switches
- Components requiring electrostatic dissipation
- Industrial and Mechanical Equipment:
- Conveyor belts
- Pump components and seals
- Precision gears and sprockets
- Consumer Goods:
- Snap-fit assemblies
- Zippers and fasteners
- Sports equipment
- Food and Beverage Industry:
- Food processing machinery parts
- Components compliant with FDA and EU regulations
- Tracing systems for contamination detection
Final thoughts on Polyoxymethylene
Polyoxymethylene, or POM, continues to be a top choice for engineers and manufacturers due to its combination of strength, stability, and machinability. Whether you’re designing components for automotive systems, industrial machinery, or consumer products, POM delivers exceptional performance across the board.
At Rex Plastics, we specialize in working with high-performance materials like POM to create precision-molded parts tailored to your unique needs. With decades of experience in injection molding, we are here to guide you through material selection, design, and production. Contact us today to learn how we can bring your project to life with POM plastic.